HOW COMPRESSED AIR SYSTEM IMPROVEMENTS CAN SAVE INDUSTRIAL OPERATIONS ENERGY & MONEY
From powering pneumatic tools to conveying materials through pipes, compressed air systems play an important role in manufacturing operations. The versatility and practicality of these systems has made them a common technology in industrial facilities of all sizes. However, there is one potential disadvantage — they can be incredibly energy intensive.
On average, 10% of most industrial energy costs are related to the electricity required to run compressed air systems. The costs associated with any inefficiencies can be difficult to manage, from increased monthly energy bills to higher operating and maintenance costs. Leaks are a common culprit and can represent 30% of compressed air loads when not managed properly.
Whether it’s properly sizing the system, identifying and eliminating leaks, maintaining and monitoring the system, or replacing it altogether, taking appropriate action now can lead to long-term energy savings and benefits. Luckily, we can make the process straightforward and more affordable — and that’s exactly how we helped Buffalo Creek Mills.
BIG SAVINGS AT BUFFALO CREEK MILLS
Buffalo Creek Mills is an oat ingredient producer of high-quality ingredients suitable for human consumption, pet food, and feed markets. This Altona-based business works in partnership with local farmers as well as buyers and distributors from Manitoba and around the world. And they’re growing rapidly, leading to increased production needs.
“As we were preparing for an expansion, our production facility’s existing compressed air system needed to be upgraded to increase its supply capacity,” said Phil Carriere, Director of Operations at Buffalo Creek Mills.
When Buffalo Creek Mills was looking to upgrade their compressed air system, we were able to help identify energy-saving opportunities by preparing a benchmark study. The project started with their contractor, Air Unlimited, performing a baseline logging of their existing compressed air system. Our industrial systems engineer then analyzed the data and prepared the benchmark study. The facility then began exploring options to optimize their compressed air system, which ultimately led to installing a new higher-efficiency compressor, a heated blower desiccant dryer with dewpoint control, oversized filters, a central regulator, and two 660-gallon storage tanks.
“We’ve already seen a difference in our energy use with these upgrades,” Carriere said. “Efficiency Manitoba estimated we’d save 356,000 kWh in electricity and $23,200 on our energy bills annually, which are huge savings for us.” These savings meant Buffalo Creek Mills received an incentive of over $41,000 from Efficiency Manitoba. “The financial and technical support Efficiency Manitoba provides through their programs was instrumental in us identifying potential improvements and designing efficient solutions for the customer,” said Juan Londono, Applications Engineer at Air Unlimited. “We knew that system control was a potential issue, and efficiency and reliability were top priorities with the new system at Buffalo Creek Mills.”
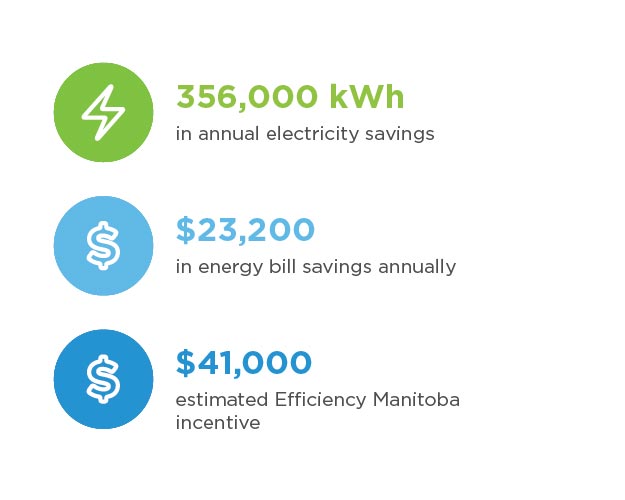
“Efficiency Manitoba was a big help in modelling the overall system reliability and energy usage. Their modelling helped to confirm that our approach for setting up the system would ensure it runs at the highest efficiency for the customer.“
— Phil Carriere, Director of Operations at Buffalo Creek Mills
WE’RE HERE TO HELP
We help forestry and mining operations make improvements to their compressed air systems by providing technical support and financial incentives. Our variety of offers can facilitate the assessment and proper sizing of new equipment, as well as the maintenance of your systems for optimal use.
We can also offset your capital investment with performance-based incentives through our Custom Energy Solutions Program. The greater the energy reduction, the higher the incentive. Our network of experienced contractors will work with customers to implement these upgrades.
If a capital upgrade isn’t in your budget, we also support energy waste reductions by addressing leaks in compressed air systems. Leak audits are an effective way to maintain and optimize your system by reducing wasted energy, minimizing unnecessary wear, and preventing operational downtime.